rugged
rotation
measurement
Up to 19 bit resolution with service free multi turn counting
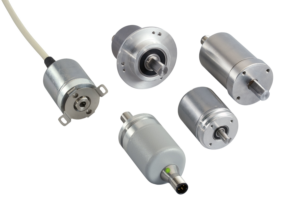
HOW DO MAGNETIC ROTARY ENCODERS WORK?
Unlocking Precision: How Magnetic Rotary Encoders Work
Magnetic rotary encoders are sophisticated devices that play a crucial role in various industries, from automotive to aerospace, robotics to manufacturing. At Osico, we’re dedicated to shedding light on the inner workings of these innovative technologies and highlighting their numerous advantages.
Principle of Operation
Magnetic rotary encoders operate based on the principle of magnetoresistance. Inside the encoder, there are two main components: a rotating shaft and a sensor assembly. Mounted to the rotating shaft is a magnet or magnet array, while the sensor assembly consists of Hall or TMR sensors positioned axial to the shaft facing the direction of magnetic flux.
As the shaft rotates, the magnetic field generated by the magnets changes in strength and orientation relative to the sensors. This change in magnetic field induces a corresponding change in the electrical resistance of the sensors, which is then detected and converted into digital signals by the encoder electronics. These signals are interpreted to determine the angular position, speed, and direction of rotation of the shaft.
Advantages of Magnetic Rotary Encoders
-
High Accuracy: Magnetic rotary encoders offer exceptional accuracy in position detection, making them suitable for applications requiring precise motion control.
-
Durability: With no physical contact between the shaft and sensor integrated circuit, magnetic encoders are highly durable and resistant to wear and tear. This ensures long-term reliability and reduces maintenance requirements.
-
Non-Contact Sensing: The non-contact sensing principle eliminates the need for mechanical components such as gears or brushes, minimizing friction and extending the lifespan of the encoder.
-
Versatility: Magnetic encoders are versatile and can be used in various environments, including those with dust, dirt, and moisture, without compromising performance.
-
High Resolution: Many magnetic encoders offer high resolution, allowing for precise measurement and control of angular position and movement.
-
Fast Response: Due to their inherent design, magnetic encoders provide fast response times, making them suitable for high-speed applications where rapid feedback is critical.
-
Compact Design: Magnetic encoders are typically compact in size, making them easy to integrate into existing systems or machinery with limited space.
Applications
Magnetic rotary encoders find applications in a wide range of industries and systems, including:
- Robotics and automation
- Machine tools and CNC machining
- Automotive and aerospace navigation systems
- Industrial machinery and equipment
- Medical devices and instrumentation
Conclusion
At Osico, we recognize the importance of magnetic rotary encoders in modern engineering and manufacturing. With their unparalleled accuracy, durability, and versatility, these devices are indispensable tools for achieving precision motion control in a variety of applications. Contact us today to learn more about our range of magnetic rotary encoders and how they can enhance your systems and processes.
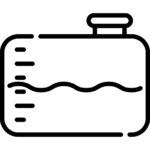
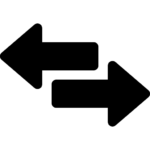
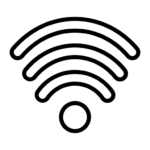
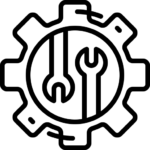
Discover our advanced high-resolution liquid level sensors tailored for Fuel, Oil, Coolant, and Water applications
Explore our durable Rotary and Linear Position sensors designed for Industrial & Off-Highway applications.
Experience IoT connectivity: monitor switches, sensors, and transmit data via GSM
Elevate industrial monitoring with our plant & machinery condition-based sensors.
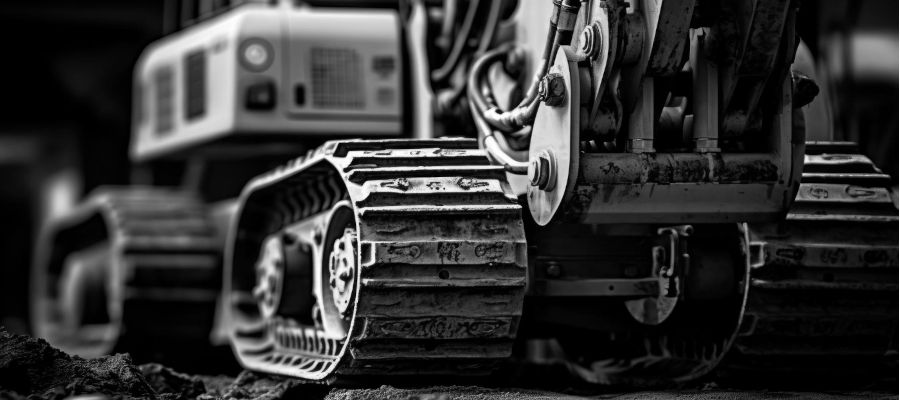
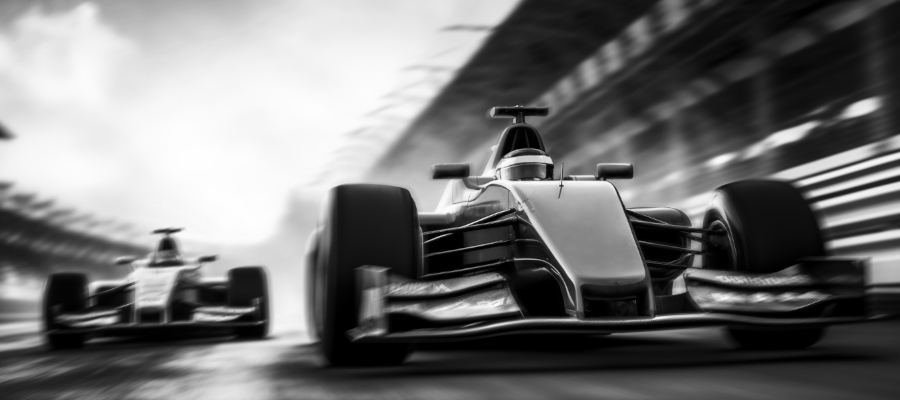